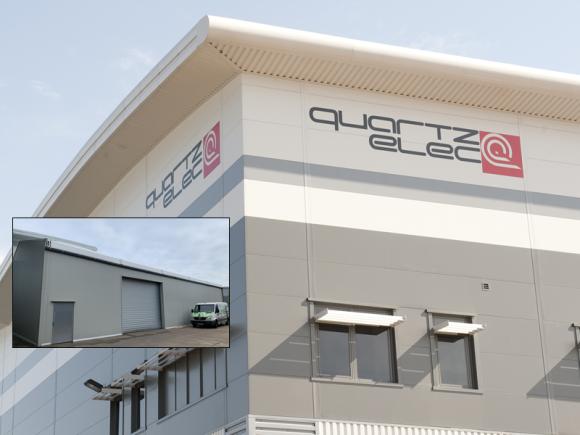
Quartzelec in Rugby is a leading engineering service business operating in the industrial, infrastructure and service sectors. Operating in the field of rotating electrical machines, they manufacture and refurbish motors and generators typically operating within the UK’s steel mills, North Sea offshore oil platforms and thermal and hydro power stations globally. It also provides products for rotating machines, coil manufacture as well as the manufacture of Quartzelec legacy machines and machine components.
An inevitable part of Quartzelec’s business involves the storage of many parts and associated pieces of equipment – often of high-value, not always required regularly and some smaller items held in quantity.
More efficient storage of parts required
With an increasingly busy shop-floor environment that was utilising every spare square metre of space, there was a distinct need identified for more effective storage of parts and spares to ensure a clutter-free work-shop and a more efficient storage solution.
Norman Emery, recently appointed Production Engineer, was responsible for producing an internal report that championed the results of effective storage and its cost-savings for the business.
“The building helps us in a number of ways”
It was clear that by removing the effects of outdoor storage where pieces had little or no protection from the elements, and allowing precision tooled equipment to be stored for long periods without any potential for physical or environmental damage, that the costs incurred in restoring items, could be saved.
“We bought the Smart-Space building to help us in a number of ways. Not only the huge potential in terms of storage space, but the additional benefits: health and safety, cost savings, quality, efficiency – it’s more than a storage facility, it is a complete package” explained Norman.
By clearing out part of the manufacturing area, 240m2 of additional space was made available - so as well as saving money, it created an opportunity for increased productivity.
Lean Manufacturing Principles
Using galvanised steel racking salvaged from the shop floor area, there was a dedicated team effort to organise the new building before passing it to the stores team to ‘sustain’. Norman explained the 5S principle used in lean manufacturing – sort, set, shine, standardise and sustain. “Our team are now seeing the benefits and we have their complete buy-in due to the fact they can see how much it has helped our day-to-day work” he added.
Quartzelec considered all multiple storage options; from a simple awning, to containers, right through to the Smart-Space option which resulted in three supplier quotes. After a visit to a similar Smart-Space installation in Nuneaton, theorder was placed.
“I am really pleased with the building. It is better than I expected” explained Norman. “The roof is particularly clever – it inflates to keep it airtight which means we don’t have any condensation. I was also expecting some water to enter at ground level but the seals in place have meant that it is completely dry.”
Use of the building is still in its infancy but there is scope to store a lot more and increase the amount of racking. There are plans to introduce a computerised stock system within the building and add final touches, such as further labelling and more yellow floor guidelines.
The project took 6 months in total from initial proposal to completion, with just 2 weeks for the actual construction.
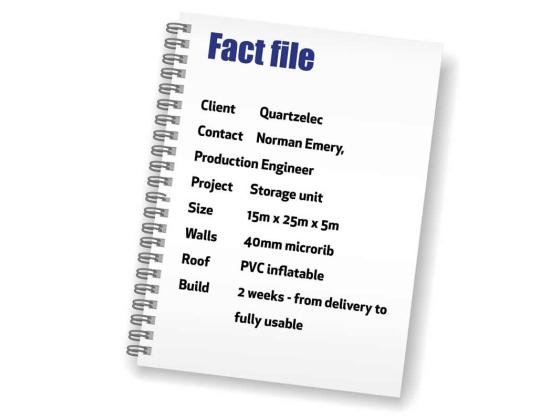
Download Quartzelec Storage Case Study

Additional storage for Quartzelec in Rugby
We bought the Smart-Space building to help us in a number of ways. Not only the huge potential in terms of storage space, but the additional benefits: health and safety, cost savings, quality, efficiency – it’s more than a storage facility, it is a complete package.
The SmartSpace team were great, looked after us from start to finish. We really appreciated the visit to a Smart-Space solution already installed and in operation – that was really valuable.
Norman Emery, Production Engineer Quartzelec